Introduction to this document
Loading bay checklist
If your business is large enough to have an allocated goods in/goods out area, it can introduce new risks into your business. So why not use a loading bay checklist to help you keep them to manageable levels?
Managing the risks
Depending on the nature and size of your business, you may have a dedicated loading bay or goods in/goods out area. If so, you need to keep an eye on those factors which can affect the health and safety of both your employees and visitors, such as delivery drivers. This is where a Loading Bay Checklist can help. Ours is divided into the sections representing the key areas that you should be looking to concentrate on.
Using the checklist
In many ways, this checklist follows the requirements of the Workplace (Health, Safety and Welfare) Regulations 1992. This is because the first four sections look at ventilation, temperature, lighting and condition of floors and traffic routes respectively. The fifth section looks at the stacking of goods and ensuring that staff follow good practices. For example, you are asked if a manual handling assessment has been carried out and if there’s sufficient room for goods to be unloaded and stored safely. Section six looks at how you organise and manage your traffic routes. This involves looking at what safety signs and markings you have in place, as well as how you’ve laid out the traffic routes. The seventh and last section concerns training and looks at what you provide in terms of safe traffic management and hazard identification.
Document
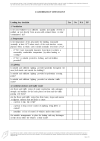
12 Dec 2009
